Robust Position Sensing for Harsh Environments
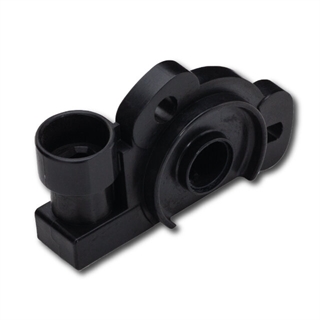
The Series 525 is a contacting rotary position sensor, designed to measure the rotational angle of rotary shafts of a multitude of applications by providing a fast and reliable analogue electric signal response. It measures the angle of a given application’s rotor shaft, and as such, it often finds use throughout the automotive market, providing vehicle engine control units with crucial information that allows for e.g., optimal dispensing of fuel.
The 525 is designed using contacting technology in which the angle of the rotary shaft determines the position of a metal contactor on a polymer resistor film, As the contactor traverses the resistor element, a variable resistance output is generated. The signal is then used by the control unit to optimize system performance.
The contacting design comes with several key advantages compared to non-contacting solutions. Contacting rotary position sensors offer stable and reliable performances over time, thanks to the mechanical contact between the sensing and moving parts. They are also better suited for harsh environment operation, displaying greater resistance to temperature fluctuations than certain non contacting options, and greater resilience against contaminating elements such as dust, dirt or oil. In addition, they are immune to electro-magnetic interference.
With more than 13 million units delivered to customers already, the series 525 is a tried-and-true rotary position solution from CTS. But the potential of the sensor extends well beyond the automotive industry. In the following, we will explore other applications which could benefit from a CTS rotary position sensor such as the series 525.
Agriculture Equipment
Equipment used for farming will naturally come into contact with a myriad of contamination agents such as dust, dirt, fertilizer, oil and other liquids. Consequently, the equipment and its constituent parts must exhibit enough robustness against these elements in order to avoid malfunctioning and excessive maintenance.
Several technical and methodological advances in agricultural practices have made robust rotary position sensors more relevant to the industry than ever before.
Automated agricultural processes are becoming ever more prevalent as the ability to respond instantly to variables such as moisture levels, temperature and wildlife can help improve crop yield.
Typically, precision agriculture is enabled by variable rate technology (VRT) which involves GPS/GNSS mapping of fields and guiding of automated equipment. Here, the need for reliable rotary position sensors is evident. In a GPS-guided tractor, for instance, rotary position sensors are used to measure the angular position of the automated steering wheel. The information provided by these sensors allows the tractor’s guiding system to make real-time adjustments to ensure accurate field navigation.
Similarly, rotary positions sensors are used for various means of implement control, tracking the positions of plows, planters and seeders. A precision seeder can employ a rotary position sensor to monitor the position of components responsible for releasing the seeds into the soil. With proper position tracking of these components, the seeds can be placed at optimal intervals and depths, contributing to improving efficiency, reducing input waste and maximizing crop yield.
Industrial Processes and Automation
In almost any industrial setting, you will find a need for reliable rotary position sensors that are capable of withstanding the inevitable exposure to dust, humidity and electromagnetic radiation.
The need manifests in human-machine interaction devices such as manual material handling equipment (cranes,
hoists, forklifts etc.) where a human-made input must be translated into a very accurate mechanical response. In such applications, high positional reliability is key in order to ensure dependable operation and to prevent inaccuracies that could lead to delays and, at worst, to work-related accidents.
The demand also becomes very apparent when considering the massive degree of movement and position coordination that goes into the automation of industrial manufacturing processes. Conveyor belts enabling many factory assembly lines are highly reliant on rotary position sensors to control the speed of the system and the placement of the items being transported on the belt. If the assembly line employs further automation, which typically would be in shape of robotic arms, these will also make use of rotary position sensors to track and control the delicate joint movement as the arms pick up, adjust and fine-tune the items in question.
Aside from assembly lines, much industrial processing machinery is contingent on rotary position sensors to properly function. In textile production, spinning machines twist fibers into yarn using several rotating axes that are closely monitored by rotary position sensors to ensure consistent
tension and yarn quality.
Similarly, weaving machines utilize the sensors for roller and drum position tracking as warp and weft yarn are interlaced to produce fabrics. The same goes for textile looms, winding, printing and knitting machines as well as fabric inspection systems.
Both contacting and non-contacting rotary position sensors can advantageously be applied in industrial settings with contacting sensors being the preferred option in harsher production environments where greater degrees of dirt and dust contamination and electromagnetic interference is present.
Off-Road Vehicles
Off-road applications are another area in which rotary position sensors are employed, and they are a common sight throughout the construction industry in particular. Booms and arms of excavators, blades of bulldozers/graders and crane booms and jibs are just a few examples of contruction vehicles and equipment where rotary position sensors play a crucial role. Exact position tracking is key in these applications as inaccuracies can be both very costly and very dangerous when heavy loads of dirt or construction materials are moved around a building site.
In the same vein, much material processing equipment is enabled by rotary position sensors. Concrete mixers use them to monitor their drum rotation in order to achieve an optimal concrete blend. Subsequently, concrete pavers will employ position sensors to ensure correct placement of paving screeds for accurate surface finishing.
In conclusion, whenever construction material is to be processed, moved or applied, chances are that a rotary position sensor help enable the equipment and vehicles being used. In this context, the advantages of a contacting rotary position sensor, such as the series 525, include its high-performance reliability and its resilience against dirt and dust contaminants that could otherwise compromise the operational safety in the already dangerous environment that is a construction site.
Conclusion
The series 525 is a versatile contacting rotary position sensor, and its applications extend well beyond the automotive industry for which it was originally conceived. Among its merits, the high degree of measuring reliability stands out and makes it a not just viable, but in many cases preferable sensor choice. This is particularly true in applications that are intended for operation in harsh environments where exposure to heat, humidity and various contamination agents are likely to occur. Under these circumstances, the series 525 exhibits great resilience and can be relied upon to provide immaculate performances.
Another major advantage of the series 525 is the simplicity of its design and operation principle which makes it easy to install across many platforms and equally effortless to maintain. This along with its competitive price point makes it a highly cost-effective solution for OEMs of several industries. It is a steady and reliable position sensing choice with short lead times, as it is available off-the-shelf from CTS’ global distribution network.