AEC-Q200 Qualified Frequency Control Products
Today’s automobile and transportation sector is seeing rapid technological developments with new applications for passenger safety, comfortability and even enjoyment being added constantly. Current vehicles are equipped with GNSS systems, infotainment, EV battery management, Advanced Drive Assistance Systems (ADAS), anti-lock braking, Automatic Emergency Braking (ABS and AEB), LiDAR and many similar features. These electronic system advancements require stable and reliable frequency control devices to operate properly. Frequency control devices such as quartz crystals and oscillators provide an internal timing reference for the electronic systems by creating a stable electrical signal at a specified frequency. This helps the systems maintain accurate signal timing for proper performance. In an automotive setting, eletronic systems face certain performance challenges which in turn calls for automotive grade crystals and oscillators.
Automotive electronic systems using frequency control devices
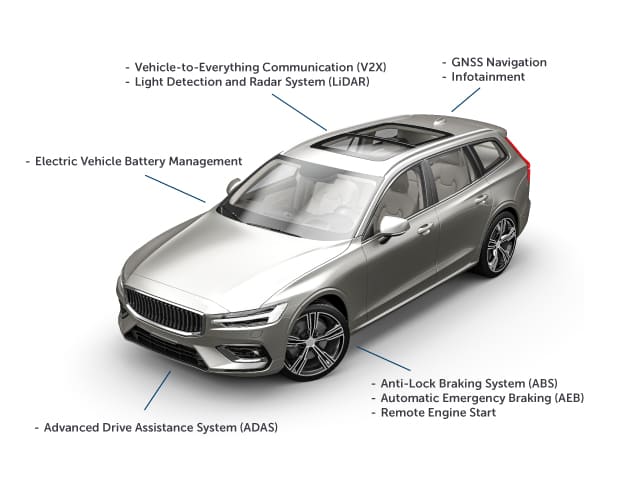
What are automotive grade crystals and oscillators?
Automotive grade crystals and oscillators are high-stability frequency control devices that are designed to operate under the high temperatures and mechanical stress that occur in an in-vehicle operational environment. Automotive grade crystals and oscillators are therefore subjected to stringent test criteria to ensure quality, safety and reliability. A device that fulfills these requirements will earn an AEC-Q200 qualification.
What is an AEC-Q200 Qualification?
AEC-Q200 is a global standard that defines stress resistance criteria for passive electronic components intended for use in automotive applications. The standard is governed by the Automotive Electronics Council (AEC) that was established in the 1990s by the major US automobile manufacturers - Chrysler, Ford and GM.
The standard provides a benchmark for the quality and reliability of passive components, ensuring that they meet the rigorous demands of automotive applications. Components must pass a series of stringent tests outlined in the AEC-Q200 standard to be deemed “AEC-Q200 qualified.” These tests assess factors like temperature, humidity, and mechanical stress.
The AEC established common part-quality system standards (AEC-Qxxx), and the most referenced documents are:
- AEC-Q100: Failure Mechanism Based Stress Test Qualification for Integrated Circuits
- AEC-Q101: Failure Mechanism Based Stress Test Qualification for Discrete Semiconductors
- AEC-Q200: Stress Test Qualification for Passive Components
The council revised AEC-Q200 to ‘Revision E’ in March 2023 that states qualification tests and in combination with JEDEC, MIL-STD and UL94 test procedures.
The following table lists the required tests for a quartz crystal. It can also be found on the AEC website. (Table 11. Table 11A allows for deviation from the stress qualifications test list. The supplier must however provide reasonable justification as to why the suggested tests do not apply.)
Test Number |
Tests |
References |
Additional Requirements |
1 |
Pre and Post Stress Electrical Test |
User Specification |
Test is performed at room temperature as specified in the applicable stressreference and the additional requirements in this table. |
3 |
High Temperature Exposure (Storage) |
MIL-STD-202
Method 108
|
Tested at maximum specified operating temperature or maximum specified storage temperature (whichever is higher). Minimum test temperature shall be 85ºC.
- 1000 hours
- Unpowered
- Measured at 24+4 hours after test conclusion
|
4 |
Temperature Cycling |
JES-D22-A104 |
- Unpowered
- 1000 cycles
- Lower temperature of the chamber: -55ºC
- Upper temperature of the chamber: Maximum specified operating temperature and shall not exceed 85ºC
- Dwell time (soak time): 15 minutes minimum / 30 minutes minimum if components weigh above 28g
- Transition time: 1 minute maximum
- Measurement at least 24 hours after test conclusion
|
7 |
Biased Humidity |
MIL-STD-202
Method 103
|
- 1000 hours
- 85ºC/85%RH
- Rated VDD applied with 1MΩ and inverter in parallel, 2x crystal CL capacitors between each crystal leg and GND
- Measurement at least 24 hours after test conclusion
|
8 |
High Temperature Operational Life |
MIL-STD-202
Method 108
|
- Note: 1000 hours
- Temperature of the chamber: Maximum specified operating temperature up to 150ºC
- Rated VDD applied with 1MΩ and inverter in parallel, 2x crystal CL capacitors between each crystal leg and GND
- Measurement at least 24 hours after test conclusion
|
9 |
External Visual |
MIL-STD-883
Method 2009
|
- Inspect devices construction, marking and workmanship
- Pre and post electrical test not required
|
10 |
Physical Dimension |
JES-D22-B100 |
- Verify physical dimensions to the applicable component specification
- Pre and post electrical test not required
|
11 |
Terminal Strength (THT) |
MIL-STD-202
Method 211
|
- Test THT component lead integrity only
- Test condition A (pull test):
Nominal Cross- Section Area (mm2) |
Force (N) |
≤ 0.05 |
1 |
0.06 to 0.10 |
2.5 |
0.11 to 0.20 |
5 |
0.21 to 0.50 |
10 |
0.51 to 1.20 |
20 |
> 1.20 |
40 |
- Test condition C (wire-bend lead test):
Section Modulus (Zx) (mm3) |
Force (N) |
≤ 1.5x10-3 |
0.5 |
1.6x10-3 to 4.2x10-3 |
1.25 |
4.3x10-3 to 1.2x10-2 |
2.5 |
1.3x10-2 to 0.5x10-2 |
5 |
0.6x10-2 to 1.9x10-1 |
10 |
> 1.9x10-1 |
20 |
- For round terminations: Zx = (πd3)/32 where d is the lead diameter
- For strip terminations: Zx = (ba2)/6 where a is the thickness of the rectangular strip perpendicular to the bending axis, b is the other dimension of the rectangular strip
- Notes: The values and formulars are per IEC 60068-2-21. 6th edition
|
12 |
Resistance to Solvents |
MIL-STD-202
Method 215
|
In addition to Method 215 solvents, add an aqueous wasah chemical and follow chemical manufacturer's recommended parameters (e.i., solutions temperature and immersion time)
- Applicable to ink-marked components and not laser-marked components
|
13 |
Mechanical Shock |
MIL-STD-202
Method 213
|
- Figure 1 of Method 213
- THT: Condition C
- SMD: Condition C
- Tested per the supplier's recommended mounting method
|
14 |
Vibration |
MIL-STD-202
Method 213
|
- 5g's for 20 minutes
- 12 cycles for each of 3 orientations
- Tested per the supplier's recommended mounting method
- Verification of transfer load: During setup, verify that with the selected PCB design (size, thickness and secured points), or an alternative mount, that the transferred load onto the components corresponds to the requested load. This verification can be achieved using a laser vibrometer or other adequate measuring device
- Test from 10 Hz to 1000 Hz
|
15 |
Resistance to Soldering Heat |
MIL-STD-202
Method 210
|
- THT: Conditions B or C
- SMD: Conditions K, time above 217ºC, 60s to 150s
- Non-soldered type mounting/attach are not applicable
|
17 |
ESD |
AEC-Q200-002 |
|
18 |
Solderability |
J-STD-002 |
- THT: Method A1, coating durability category 2
- SMD: Method B1, coating durability category 2 or Method D, coating durability category 2
- Notes: In particular circumstances when SnPb reverse compatibility is requested by the user, Method A shall be used for THT and Method B shall be used for SMD
- Magnification 50x
- Pre and post electrical test not required
- Non-soldered type mounting/attach are not applicable
|
19 |
Electrical Characterization |
User Specification |
- Parametrically test per lot and sample size requirements
- Summary to show minimum, maximum mean an standard deviation at room, minimum and maximum temperatures
- Pre and post electrical test not required
|
20 |
Flammability |
UL-94 or IEC 60695-11-5 |
- Applicable to components with exposed cured resins or plastic materials
- If exposed resins or plastic materials are V-1, V-0 or 5VA, testing is not required
- If exposed resins or plastic materials are not V-1, V-0 or 5VA, components or applicable parts of the component (e.g., sleeve or enscapsulant), material shall be tested to the Needle Flame test per IEC 60695-11-5. Data from previously qualified materials can be supplied in place of conducting test
- Pre and post electrical test not required
|
21 |
Board Flex |
AEC-Q200-005 |
|
22 |
Terminal Strength (SMD) |
AEC-Q200-006 |
|
Notes: For any deviation from the above stresses, refer to section 2.4.8.
Back to Table C: Qualification Sample Size
Back to Table D: Applicable Stress Conditions
|
CTS automotive grade clock oscillators (AEC-Q200 certified)
Features:
- AEC-Q200 Certified
- PPAP Compliant
- Operating Temperature: -40ºC to 125ºC
- HCMOS; LVPECL or LVDS Complementary Outputs
- HCMOS Output
- Complimentary Outputs (LVPECL and LVDS)
- Small Package Footprints
Applications
- Automotive Electronics
- Infotainment and Audio/Video Systems
- Mobile Multimedia Systems
- Medical Electronics
- Commercial Aerospace/Defense
- Industrial IoT
- M2M Communication
- Industrial Controls and Automation
- Test and Measurement
Model |
Features |
Package |
Size |
Output |
Frequency |
Phase Jitter |
Frequency Stability |
Supply Voltage |
Temp Range |
CA20C |
Low Jitter
Output Enable
Fund & 3rd OT
|
SMD, 4-Pad
Leadless Castellated Ceramic
|
2.0 x 1.6 mm |
HCMOS |
1.25 - 100 MHz |
Typical: 0.5 PS Max
Max: < 1.0 PS Max |
±25ppm
±30ppm
±50ppm
±100ppm
±150ppm |
1.8V
2.5V
3.3V
|
-40°C to 85°C
-40°C to 105°C
-40°C to 125°C
-55°C to 105°C |
CA25C |
Low Jitter
Output Enable
Fund & 3rd OT
|
SMD, 4-Pad
Leadless Castellated Ceramic
|
2.5 x 2.0 mm |
HCMOS |
1.25 - 156.25 MHz |
Typical: 0.5 PS Max
Max: < 1.0 PS Max |
±25ppm
±30ppm
±50ppm
±100ppm
±150ppm |
1.8V
2.5V
3.3V
|
-40°C to 85°C
-40°C to 105°C
-40°C to 125°C
-55°C to 105°C |
CA25P
CA25L
|
Low Jitter
Output Enable
Fund & 3rd OT
|
SMD, 6-Pad
Leadless Castellated Ceramic
|
2.5 x 2.0 mm |
LVPECL
LVDS
|
13.5 - 160 MHz |
Max: 0.5
PS Max |
±25ppm
±30ppm
±50ppm
±100ppm
±150ppm |
1.8V
2.5V
3.3V
|
-40°C to 85°C
-40°C to 105°C
-40°C to 125°C |
CA32C |
Low Jitter
Output Enable
Fund & 3rd OT
|
SMD, 4-Pad
Leadless Castellated Ceramic
|
3.2 x 2.5 mm |
HCMOS |
1.25 - 156.25 MHz |
Typical: 0.5 PS Max
Max: < 1.0 PS Max |
±25ppm
±30ppm
±50ppm
±100ppm
±150ppm |
1.8V
2.5V
3.3V
|
-40°C to 85°C
-40°C to 105°C
-40°C to 125°C
-55°C to 105°C |
CA32P
CA32L
|
Low Jitter
Output Enable
Fund & 3rd OT
|
SMD, 6-Pad
Leadless Castellated Ceramic
|
3.2 x 2.5 mm |
LVPECL
LVDS
|
13.5 - 160 MHz |
Max: 0.5
PS Max |
±25ppm
±30ppm
±50ppm
±100ppm
±150ppm |
1.8V
2.5V
3.3V
|
-40°C to 85°C
-40°C to 105°C
-40°C to 125°C |
CA50C |
Low Jitter
Output Enable
Fund & 3rd OT
|
SMD, 4-Pad
Leadless Castellated Ceramic
|
5.0 x 3.2 mm |
HCMOS |
1.25 - 156.25 MHz |
Typical: 0.5 PS Max
Max: < 1.0 PS Max |
±25ppm
±30ppm
±50ppm
±100ppm
±150ppm |
1.8V
2.5V
3.3V
5.0V
|
-40°C to 85°C
-40°C to 105°C
-40°C to 125°C
-55°C to 105°C |
CA50P
CA50L
|
Low Jitter
Output Enable
Fund & 3rd OT
|
SMD, 6-Pad
Leadless Castellated Ceramic
|
5.0 x 3.2 mm |
LVPECL
LVDS
|
13.5 - 160 MHz |
Max: 0.5
PS Max |
±25ppm
±30ppm
±50ppm
±100ppm
±150ppm |
1.8V
2.5V
3.3V
|
-40°C to 85°C
-40°C to 105°C
-40°C to 125°C |
CA70C |
Low Jitter
Output Enable
Fund & 3rd OT
|
SMD, 4-Pad
Leadless Castellated Ceramic
|
7.0 x 5.0 mm |
HCMOS |
1.25 - 156.25 MHz |
Typical: 0.5 PS Max
Max: < 1.0 PS Max |
±25ppm
±30ppm
±50ppm
±100ppm
±150ppm |
1.8V
2.5V
3.3V
|
-40°C to 85°C
-40°C to 105°C
-40°C to 125°C
-55°C to 105°C |
CA70P
CA70L
|
Low Jitter
Output Enable
Fund & 3rd OT
|
SMD, 6-Pad
Leadless Castellated Ceramic
|
7.0 x 5.0 mm |
LVPECL
LVDS
|
3.5 - 160 MHz |
Max: 0.5
PS Max |
±25ppm
±30ppm
±50ppm
±100ppm
±150ppm |
1.8V
2.5V
3.3V
|
-40°C to 85°C
-40°C to 105°C
-40°C to 125°C |
CTS automotive grade crystals (AEC-Q200 certified)
Features:
- AEC-Q200 Certified
- PPAP Compliant
- Small Package Footprints
- Extended Operating Temperature to 125ºC
- Temperature Stability Reaching ± 15ppm
Applications
- Remote Keyless Entry (RKE)
- Infotainment and Audio/Video Systems
- Mobile Multimedia Systems
- Medical Electronics
- Commercial Aerospace/Defense
- Bluetooth, ZigBee, Wi-Fi
- Tire Pressure Monitoring System (TPMS)
- Industrial IoT
- M2M Communication
- Industrial Controls and Automation
- Test and Measurement
- Wireless Communication
Model |
Package |
Size |
Frequency |
Frequency Tolerance at 25ºC |
Frequency Stability |
Temp Range |
HTA |
SMD Metal Can
|
11.10 x 4.83 x 4.30
mm |
3.2 - 65 MHz |
±10ppm
±15ppm
±20ppm
±25ppm
±30ppm |
±15ppm
±20ppm
±25ppm
±30ppm
±50ppm
±100ppm
±150ppm |
-40°C to 85°C
-40°C to 105°C
-40°C to 125°C
-55°C to 105°C |
SA164 |
SMD, 4-Pad Seam Seal
|
1.6 x 1.2 x 0.40
mm |
24 - 60 MHz |
±10ppm
±15ppm
±20ppm
±25ppm
±30ppm |
±15ppm
±20ppm
±30ppm
±50ppm
±100ppm
±150ppm |
-40°C to 85°C
-40°C to 105°C
-40°C to 125°C
-40°C to 150°C
-55°C to 105°C
-55°C to 125°C |
SA204
|
SMD, 4-Pad Seam Seal
|
2.0 x 1.6 x 0.5
mm |
16 - 96 MHz |
±10ppm
±15ppm
±20ppm
±25ppm
±30ppm |
±15ppm
±20ppm
±30ppm
±50ppm
±100ppm
±150ppm |
-40°C to 85°C
-40°C to 105°C
-40°C to 125°C
-40°C to 150°C
-55°C to 105°C
-55°C to 125°C |
SA254 |
SMD, 4-Pad Seam Seal
|
2.5 x 2.0 x 0.65
mm |
12 - 80 MHz |
±10ppm
±15ppm
±20ppm
±25ppm
±30ppm |
±15ppm
±20ppm
±30ppm
±50ppm
±100ppm
±150ppm |
-40°C to 85°C
-40°C to 105°C
-40°C to 125°C
-40°C to 150°C
-55°C to 105°C
-55°C to 125°C |
SA324
|
SMD, 4-Pad Seam Seal
|
3.2 x 2.5 mm |
8 - 160 MHz |
±10ppm
±15ppm
±20ppm
±25ppm
±30ppm |
±15ppm
±20ppm
±30ppm
±50ppm
±100ppm
±150ppm |
-40°C to 85°C
-40°C to 105°C
-40°C to 125°C
-40°C to 150°C
-55°C to 105°C
-55°C to 125°C |
SA532 |
SMD, 2-Pad Seam Seal
|
5.0 x 3.2 x 1.1
mm |
7.6 - 160 MHz |
±10ppm
±15ppm
±20ppm
±25ppm
±30ppm |
±15ppm
±20ppm
±30ppm
±50ppm
±100ppm
±150ppm |
-40°C to 85°C
-40°C to 105°C
-40°C to 125°C
-40°C to 150°C
-55°C to 105°C
-55°C to 125°C |
SA534
|
SMD, 4-Pad Seam Seal
|
5.0 x 3.2 x 0.85
mm |
7.6 - 160 MHz |
±10ppm
±15ppm
±20ppm
±25ppm
±30ppm |
±15ppm
±20ppm
±30ppm
±50ppm
±100ppm
±150ppm |
-40°C to 85°C
-40°C to 105°C
-40°C to 125°C
-40°C to 150°C
-55°C to 105°C
-55°C to 125°C |
TFA16 |
SMD- 2-Pad Hermetic Ceramic
|
1.6 x 1.0 x 0.5
mm |
0.032768 MHz |
±10ppm
±20ppm |
-0.034ppm/°C2
Temp Coefficient |
-40°C to 85°C
-40°C to 105°C |
TFA20
|
SMD- 2-Pad Hermetic Ceramic
|
2.0 x 1.2 x 0.6
mm |
0.032768 MHz |
±10ppm
±20ppm |
-0.034ppm/°C2
Temp Coefficient |
-40°C to 85°C
-40°C to 105°C |
TFA32
|
SMD- 2-Pad Hermetic Ceramic
|
3.2 x 1.5 x 0.9
mm |
0.032768 MHz |
±10ppm
±20ppm |
-0.034ppm/°C2
Temp Coefficient |
-40°C to 85°C
-40°C to 105°C |