Enabling Underwater Exploration and Seabed Analysis
An echosounder is a sonar device used to map underwater objects and topography. Capable of locating and describing targets in the water and on the seafloor using sound waves, echosounders are used for depth measurement, inspection of underwater structures, search and rescue operations and scientific exploration. Whereas singlebeam echosounders only provide information about the depth of the waters, their multibeam counterparts can grant a full seabed profile for a more detailed analysis. Piezoelectric components and transducers are an essential part of sonar systems and are crucial in enabling high-performance multibeam echosounders.
How do multibeam echosounders work?
Multibeam echosounders operate according to the sonar principle where a narrow pulse of acoustic waves is generated by means of the converse piezoelectric effect and directed towards the ocean bottom. The waves are then reflected back by either the seafloor or objects in the water and subsequently registered again by the echosounder, converting them into electric signals through the direct piezoelectric effect.
Multibeam echosounders typically rely on two types of piezoelectric transducers to achieve this: A high-power transducer to generate and transmit the acoustic wave and an array of highly sensitive receiving transducers that register the reflected waves and convert them into electric signals. By looking at the amplitude of the waves and the time difference between the received signals, processing electronics apply imaging principles to generate a 2D section (swath) with detailed information of the surveyed area. More advanced systems use scanning or complex receiver arrays and are capable of generating a 3D image instead. Depending on the distance the sound has to travel, and spatial resolution that is required, multibeam echosounders will operate at frequencies between 50kHz and 800kHz.
Which piezo elements can be used for multibeam echosounder receivers?
Receivers for underwater imaging are usually fitted with piezoelectric components made of a PZT piezoceramic material with properties ranging from semi-soft (NCE51, Pz27, 3195STD) to soft (NCE56, Pz29, 3203STD). The components can have various shapes and sizes depending on the application, but the most common design is a simple plate. Large plates can be made into composites for increased sensitivity, while smaller plates can be assembled into arrays. CTS delivers single elements of piezoceramic blocks in sizes up to 150x100mm with uniform properties, but also offers dicing and upper-level assembly including arrays of sensitive piezo elements, ready for further integration.
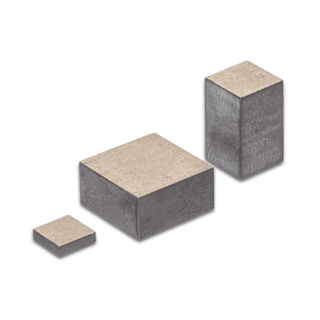
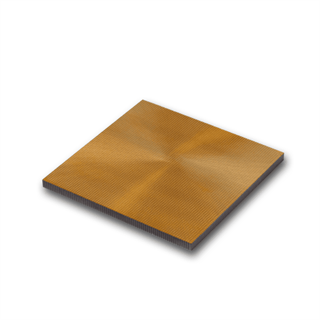
Piezoceramic Materials for Multibeam Echosounder Receivers |
Parameter |
Semi-Soft Navy Type II |
Soft Navy Type VI |
Example Material |
NCE51 |
3203STD |
Relative Permittivity K33s |
1900 |
3250 |
Coupling kt (Plate Thickness) |
50% |
56% |
Coupling k33 (Composite) |
74% |
70% |
Piezoelectric Charge Coefficient d33 |
443 pC/N |
530 pC/N |
Mechanical Quality Factor Qm |
80 |
50 |
Curie Temperature TC |
360ºC |
225ºC |
Custom Solutions and Value-Add Options
Each customer that CTS partners with, has unqiue needs that might require a customized product solution. Our internal team of engineers and product experts work directly with customers in designing solutions that meet demanding specifications. Typical customization options and value-add opportunities for piezoceramic receivers in multibeam echosounder applications include:
• Thickness or frequency tolerance: Piezoceramic components can be manufactured to a certain size or tuned to a specific resonance frequency. Thickness can be adjusted to match either tight frequency or mechanical tolerances. Sonar receivers are typically tied to a given frequency, and a frequency tolerance down to ±2% and a dimensional tolerance down to ±0.05mm allow for a low batch-to-batch dispersion for consistent operation of the array.
• Composite manufacture: CTS has the capabilities to design and manufacture piezoceramic composites that can be directly integrated in a sonar system. 1-3 composites achieve a higher electromechanical coupling and a wider bandwidth than bulk piezoceramics.
• Worldwide Manufacture: With manufacturing locations in North America, Europe and Asia, CTS can better service customers close to our facilities and reduce supply risks.