Principles of Operation and Ideal Applications
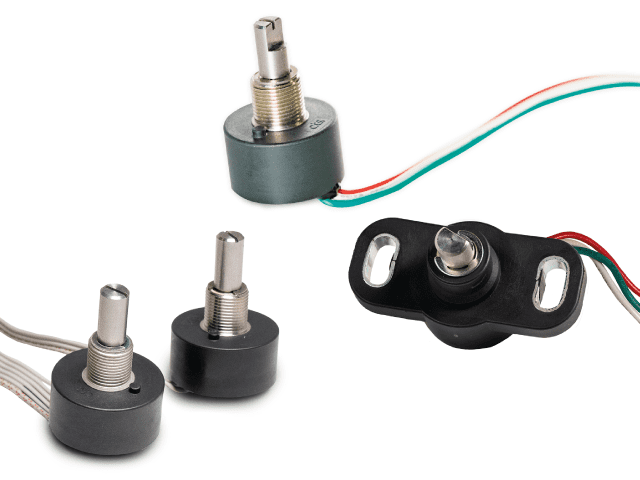
Hall-effect Rotary Position Sensors are electro-mechanical devices, used to measure the displacement and position of an object. They are capable of determining angles of rotation by providing feedback in form of a linear signal output which makes them highly suitable for various applications where precise measurement of angular position is essential.
While some rotary position sensors utilize contacting elements such as a wiper to generate an output signal, these devices are non-contacting thanks to their operating principle and namesake, the Hall-effect.
What is the Hall-effect, and how is it utilized?
The Hall-effect refers to the electrical potential difference across a conducting or semi-conducting material when it is subjected to a magnetic field perpendicular to the direction of the current flow. As current passes through the conductor, the magnetic field will bend the electrons to one side, creating a voltage difference across the conductor’s surface.
A typical Hall-effect rotary position sensor consists of a magnetic disk attached to a rotating shaft and a stationary integrated circuit sensing element. As the magnetic disk rotates, it causes a change in the voltage across the sensing element, proportional to the strength and polarity of the magnetic field. The voltage is then used to determine the exact angular position of the target object relative to the sensor’s reference point.
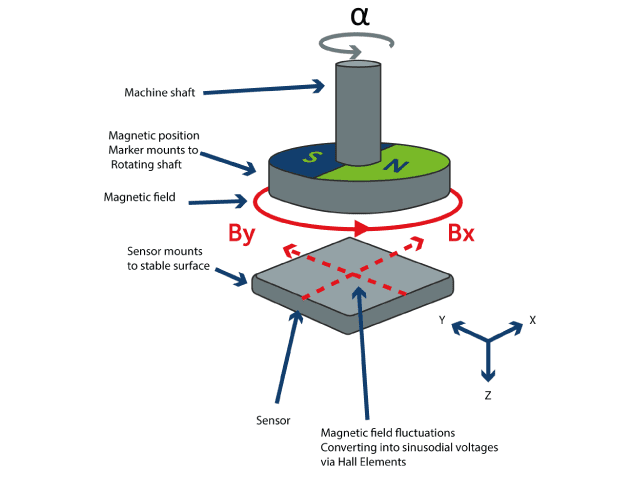
Advantages of Hall-effect rotary position sensors
Hall-effect rotary position sensors generally offer a good blend of accuracy and resolution. They produce an analogue output similar to contacting potentiometers, but do so without the aid of physical wiper contact. With no internal contacting parts, these sensors are not subjected to the same degree of mechanical wear and tear as their contacting counterparts, resulting in much longer rotational life spans. As such, applications utilizing non-contacting Hall-effect technology are likely to have their rotational life extended by a factor of at least 20. This also greatly reduces the need for maintenance and service replacement, translating to cost-savings in the long run.
Additionally, Hall-effect rotary position sensors can operate reliably in a wide temperature range, and they are largely unaffected by humidity or dry environments. Shock and vibration exposure has little detrimental effect on their performance, making them excel in static and dynamic applications that operate in harsh, hazardous and/or dirty environments.
Finally, Hall-effect rotary position sensors are often compactly built and can be designed in various factor forms, offering great flexibility. These features make them highly suitable for applications where space restriction is a factor to consider. Overall, Hall-effect rotary position sensors are flexible, reliable and cost-effective with the price range directly tied to the accuracy and rotational life specifications.
Ideal applications of Hall-effect rotary position sensors
Material Handling Applications where careful positioning and placement of goods, materials and valuables are essential, e.g., fork lifts, cranes and platform trucks, will greatly benefit from implementing Hall-effect rotary position sensors. Asthese applications often operate in locations with varying degrees of environmental influence such as docksides, construction sites, airports and warehouses, the temperature, and vibration resilience of Hall-effect rotary position sensors will certainly come in handy. At the same time, these sensors will provide more than sufficient accuracy and resolution to complete associated tasks - with the added benefits of reducing calibration, maintenance and equipment down time.
Process Automation
Non-contacting rotary position sensors utilizing the Hall-effect are the ideal choice for several process automation applications. Examples of this are valve controllers and actuators, where the sensors enable remote actuation and flow adjustment, and automated robotics systems, where the sensors are used to provide feedback on the position of robotic arms, grippers and other moving parts, ensuring accurate and safe operation. For automated assembly lines where welding and/or soldering are performed, the sensors are also a good positioning solution thanks to their high temperature resistance and overall sturdiness.
Off-Road and Marine Transportation
Hall-effect rotary position sensors often find use in off-road transportation such as construction vehicles and agriculture equipment where they are deployed in e.g., throttle body and position sensing. Their non-contacting nature makes them capable of withstanding great amounts of vibrational forces which is a common occurrence in these fields. Marine applications include boat throttle controls, ship propulsion and rudder position feedback. In challenging sea environments, these sensors provide reliable operation despite changing temperatures and influence of the elements. Their compact design also allows for easy system integration without the need for drastic changes to the overall architecture.
Medical
Applications in the medical field typically include patient table positioning for laser treatment, radiation and/or x-ray as well as patient chairs for laser surgery and dental work. Non-contacting Hall-effect rotary position sensors can provide the accuracy and reliable performance which many high-precision medical procedures are contingent on. The long rotational life cycles and general durability of these products are also greatly beneficial across the global healthcare systems as reduced equipment maintenance and down time will help shortening treatment waiting times.